
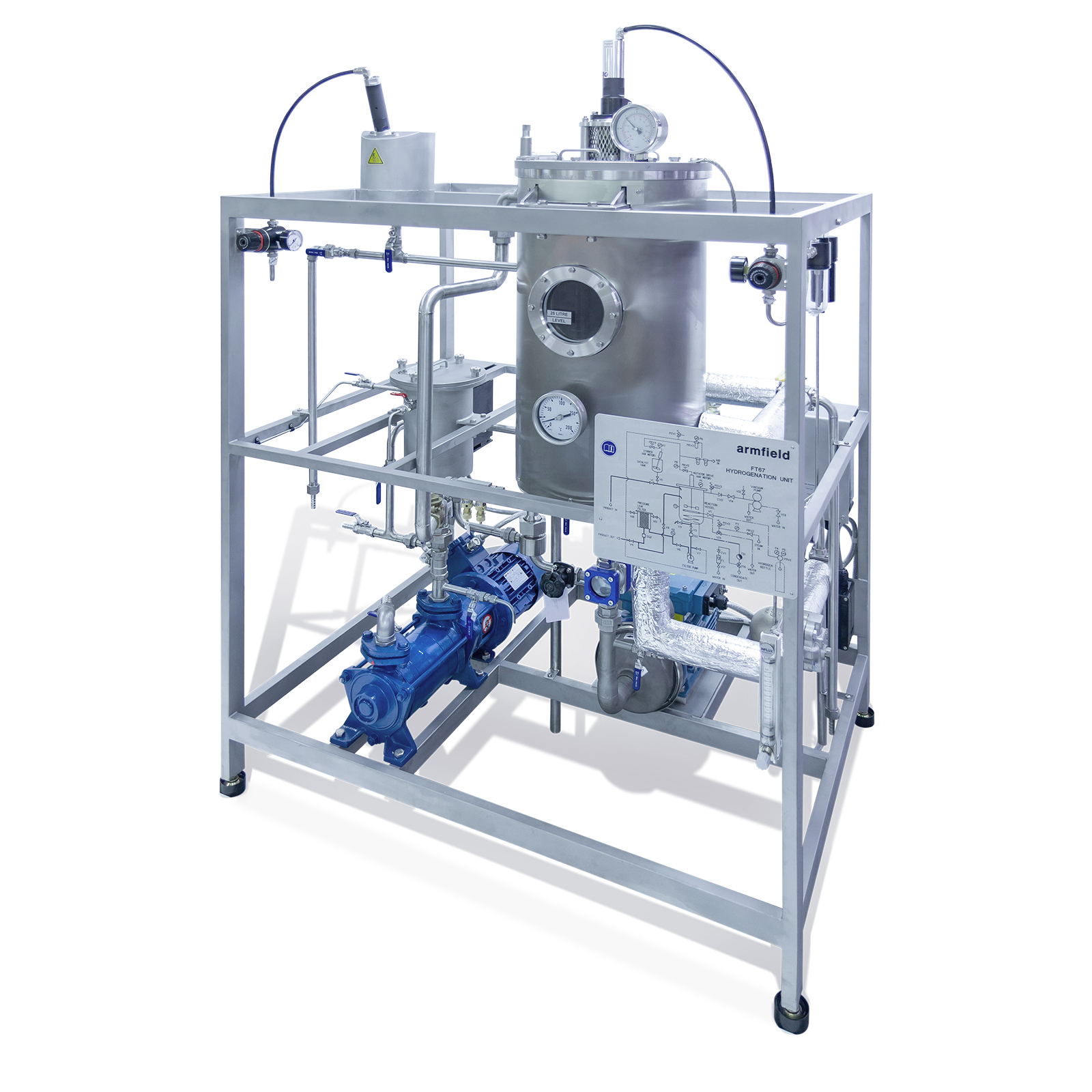
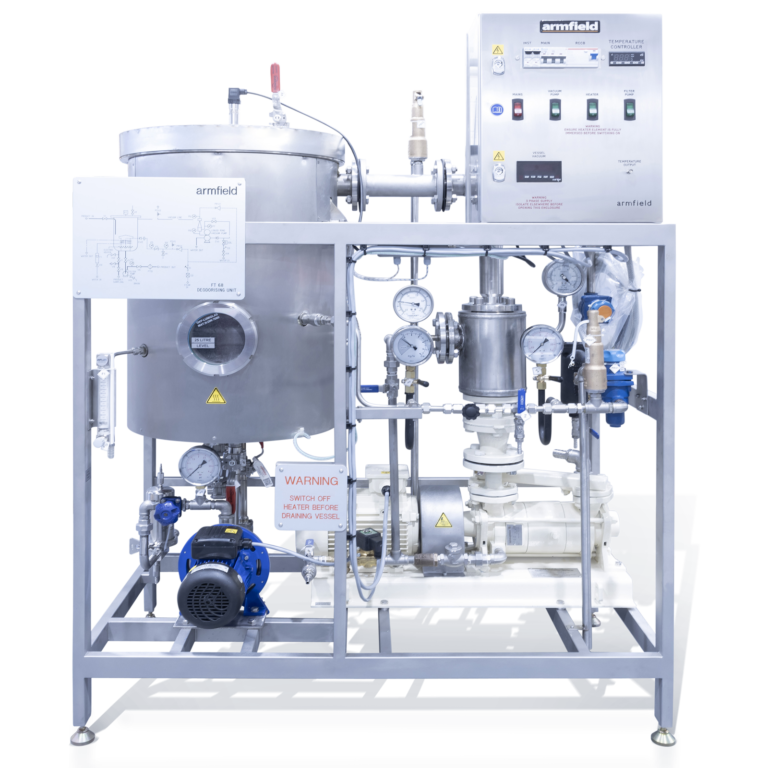
FT66 Neutraliser/Washer/Bleacher
28 มีนาคม 2566
ผู้ชม 672 ผู้ชม
Summary
The main reactor vessel, reagent vessels, filter pump and filter are constructed from stainless steel and are mounted within a floor-standing, stainless steel framework. A variable speed agitator, electrical heating element, cooling coil and observation port are incorporated in the reactor, which is a vertical cylindrical vessel designed to process a 25 litre batch of oil.
A liquid ring vacuum pump, also mounted within the framework, is used to create the desired vacuum in the vessel.
Processing under reduced pressure prevents oxidation of the oil and promotes drying. Vacuum suction is also used to charge the reactor with crude oil and to add reagents and bleaching earth from the appropriate vessels. The reagent tank is used to make up caustic solutions and other additives and to preheat to the desired temperature prior to addition to the reactor. Water for the washing process is also preheated in this vessel. The heating element in the reagent tank is controlled automatically by an electronic controller in the control console. The desired operating temperature of the reactor vessel contents is achieved using an immersed electrical heating element with a maximum power input of 3kW. The heating operation is controlled using a digital display electronic controller, which automatically maintains the temperature.
Cooling of the hot oil is achieved by circulating cold water through a submerged coil. A flat blade agitator in the reactor is driven by a geared electric motor and the speed of the motor can be adjusted up to a maximum of 1800rpm using a potentiometer on the console. Agitation of the oil charge promotes mixing of reagents and adsorbents with the oil as well as increasing heat transfer efficiency of the heating and the cooling cycles.
The bleaching earth hopper is a steep sided conical vessel designed to enable dosing of the required amount of bleaching earth into the reactor. It is also used for the addition of other adsorbents such as activated carbon. Diatomaceous earth can be charged from this hopper as an aid for the filtering process.
A stainless steel centrifugal pump is used to transfer the oil to the filter in order to filter out any solids previously added. The filter is a pressure leaf type, which is designed for repeated use with no consumable filter elements required. By recirculating the oil/ adsorbent mixture through the filter, a layer of solids is built up on the filter mesh screen upon which the remaining solids are deposited. When the oil is clear, it is discharged from the reactor through the filter after which the ‘filter cake’ is dried using compressed air so that it can be removed easily from the filter screen.
Application
food industry
Example product, palm oil, essential oils, vegetable oil
Specification
Technical Specification | Description |
Reactor Vessel | |
Material | Stainless steel |
Total volume | 45 litres |
Working volume | 25 litres |
Diameter | 0.30m |
Height | 0.65m |
Heating element | 3.0kW |
Cooling coil area | 0.12m² |
Agitator speed | 250-1800rpm |
Reagent Vesse | |
Material | stainless steel |
Working volume | 3 litres |
Diameter | 0.165m |
Height | 0.20m |
Heating element | 1kW |
Earth Hopper | |
Material | Stainless steel |
Volume | 0.3 litre |
Pressure Leaf Filter | |
Material | stainless steel |
Filter volume | 3.8 litres |
Filter cake capacity | 1 litre |
Filtering area | 0.09m² |
Filter screen | 110 mesh (0.3mm wire) |
Maximum pressure | 3.0 bar |
Vacuum Pump | |
Type | liquid-ring |
Sealant | water |
Working vacuum | 75mm Hg (ABS) |
Sealant flow rate | 8 l/m |