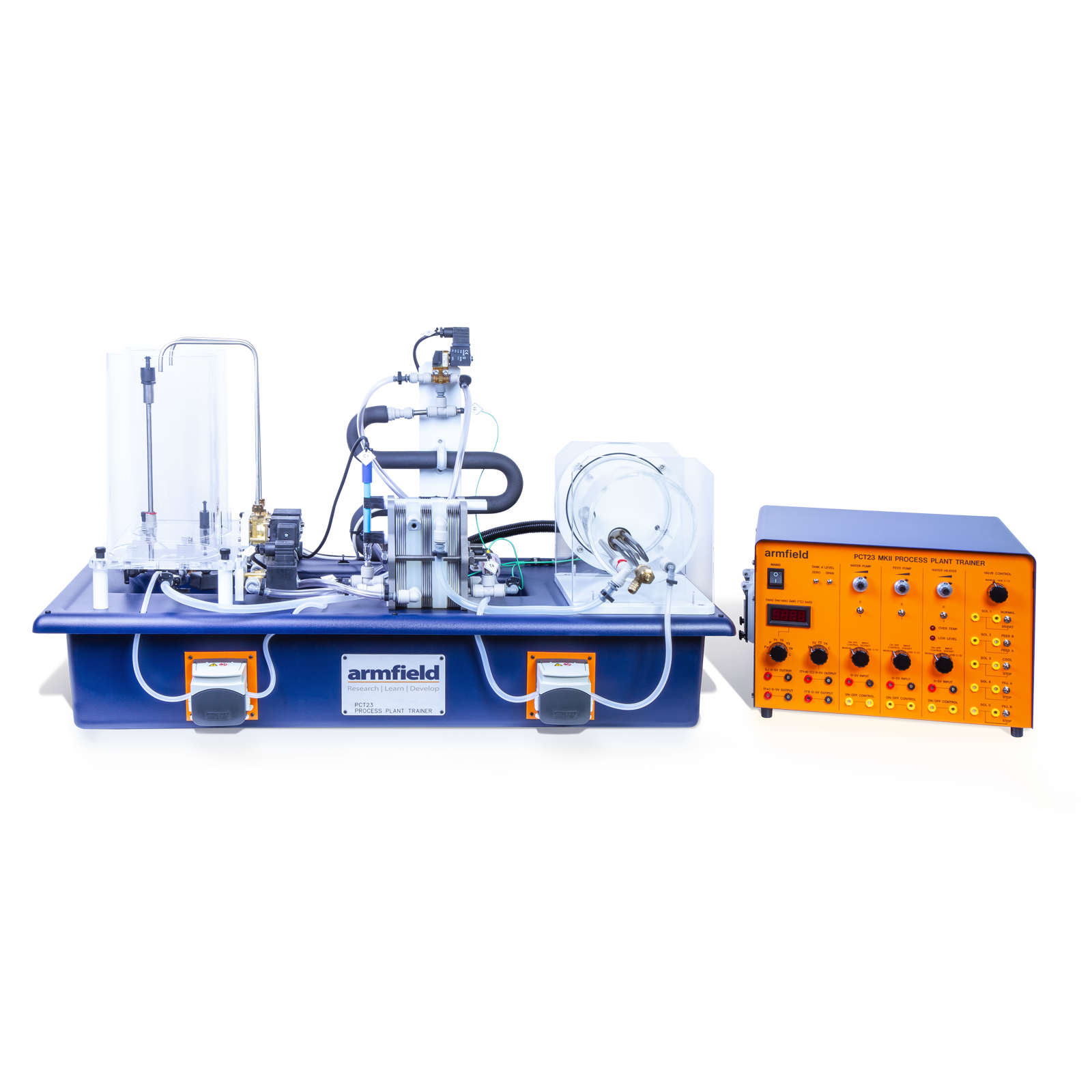
Process Plant Trainer
19 เมษายน 2566
ผู้ชม 527 ผู้ชม
DESCRIPTION
The Armfield Process Plant Trainer – PCT23MKII can be used to demonstrate a complete range of process control methods and strategies. Manual control and single feedback loops through to sophisticated cascade loops can be demonstrated along with distributed supervisory control of the whole process, by a remotely located computer.
The system is a miniature replication of a true production process. The student is presented with real process control problems with realistic dynamic behaviour and instabilities.
EXPERIMENTAL CONTENT – PCT23
Practical training exercises
The Armfield PCT23MKII Process Plant trainer is designed to cover course topics ranging from a first introduction to the subject of process control through to demonstrations of the latest advanced techniques including the use of online mathematical models.
Plant Monitoring using a PC – Gaining familiarity with computer-based mimic diagrams for monitoring process variables: level, temperatures, flows and power.
Calibration of Sensors – To calibrate the level sensor installed on the Process Plant Trainer.
Process Dynamics I
- Steady State Operation (Direct Heating) – Introducing a first order system and the achievement of steady state by investigating the hot water tank characteristics (observing the effect of constant direct heating on the temperature in the hot water tank)
- Indirect Heat Exchange – Demonstrating indirect heating using a plate heat exchanger
- Dead Time – Demonstration of the phenomenon of dead time
- Step Changes – Measuring the response of a system (the plate heat exchanger) to step changes
- Heat Transfer Losses – To calculate heat transfer losses for the system
Process Dynamics II
- Interaction – Demonstrating the interaction between different loops in the system.Understanding how changing one process variable (e.g. flow rate) affects all the others (eg. temperatures)
- Heat Regeneration – From both environmental and economic viewpoints, recycling or regeneration of energy within the process is desirable. The heat exchanger on PCT23 is equipped with a regeneration section where incoming cold feed is preheated by outgoing hot product
- Indirect Cooling – In some situations, the finished product will need to be cooled further for final storage even after giving up energy in the regeneration section of the heat exchanger. The heat exchanger on PCT23 is equipped with a cooling section where outgoing roduct can be indirectly cooled using cold water (or chilled water)
- Process Duty – Understanding process duty and temperature differentials in the heat exchanger
- PID Control of Level using Software – Introduction to level control using a PC (single loop PID controller in software)
- PID Control of Flow using Software – Introduction to flow control using a PC (single loop PID controller in software)
- PID Control of Temperature using Software – Introduction to temperature control using a PC (single loop PID controller in software)
- PID Control of Conductivity using Software -To control the conductivity of the final product by adding a salt solution to the feed
- Indirect PID Control of Temperature – To demonstrate single loop PID control
- PID Control of Temperature with Dead Time – To demonstrate single loop PID control, with product temperature controlling heater power
- PID Control with Alarm Driven Disturbances – To demonstrate the effect on control action of including an alarm-activated diverter valve
- Controller Optimisation – Determining the ideal control parameters for a simple system (single loop, temperature to heater power)
- Controller Optimisation with Dead Time – Determining the ideal control parameters for a simple system with dead time (single loop, temperature to heater power)
- Two Loop Cascade Control – To demonstrate cascade control, whereby product temperature controls hot water temperature set point, which in turn controls heater power
- Two Loop Control and Interaction – To demonstrate the effect on process response of two separate PID control loops which interact
- Three Loop Control – To demonstrate multivariable control with interacting and non-interacting loops
- Fault Finding and Diagnostics – Fault simulation and diagnosis by the instructor switching out selected signals
WITH OPTIONAL PCT20H INDUSTRIAL CONTROLLER
- External Level Controller Setup
- External On/Off Level Control
- External Time-Proportioned Level Control
- External PID Level Control
- External Flow Controller Setup
- External On/Off Flow Control
- External Time-Proportioned Flow Control
- External PID Flow Control
- External Temperature Controller Setup
- External On/Off Temperature Control
- External Time-Proportioned Temperature Control
- External PID Temperature Control
- Alarm Functions
- Comparison of Control Requirements
- Manual Tuning of a PID Controller
- Automatic Tuning of a PID Controller
TECHNICAL SPECIFICATIONS
FLOW RATE RANGES
- Product stream: 0-480ml/min
- Washing reagent: 0-480ml/min
- Heating fluid: 0-600ml/min
- Max. temperature of heating fluid: 80°C
- Heat exchanger: Plate type
- Feed and reagent vessel capacity: 5.7 litres (each)
- Heating vessel capacity: 3.7 litres
- Signal voltages: 0-5V
- Level sensor range: 0-250mm
- Flow sensor range: 0-500ml/min
- Temperature sensor range: 0-100°C
(all 0-5V dc output) PCT19BR Industrial PLC Unit
SAFETY FEATURES
RCD in the console, all circuits protected by MCB’s, 24V dc operation of solenoid valves and pump motors
Heating vessel
- Thermostat limiting max temp
- Low level switch
- Vent to avoid pressurisation
FEATURES & BENEFITS
The Armfield Process Plant Trainer is a miniature version of a real industrial process, having typical problems of dynamics and stability for which control strategies must be devised and operated.
The following process characteristics are incorporated:
- Multiple inputs and outputs
- Presence of dead time
- Recycling to minimise energy needs
- Alarms with corrective actions
- Operational sequencing from start up to shut down
The trainer allows the user to investigate various control techniques associated with process plant. These techniques range progressively from single loop analogue control through to multi loop PLC systems and ultimately to distributed supervisory control of the whole process by a remotely located PC station.
The Process Plant Trainer incorporates an electrical console which provides access to the various signals associated with measurement and control of the process allowing a variety of control possibilities:
- Manual operation
- Data logging using a PC or chart recorder
- Manual control via a PC using a mimic diagram
- Direct digital control using a PC
- Use of industrial, PID or programmable controllers
- Use of customer-provided controllers
- Use of serial communications for supervisory control of individual controllers (SCADA)