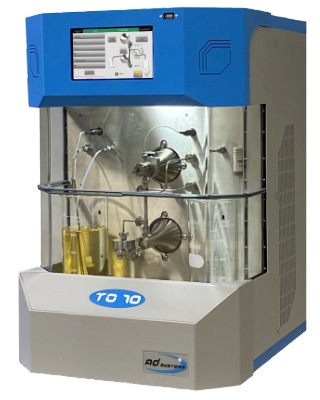
Summary
The ASTM D3241 / IP 323 Thermal Stability test is one of the most important tests for the jet fuel quality. This test method was inherently limited due to the subjectivity in the color standard for tube deposit rating
Recently advanced testing metrics (called metrological method) for quantifying the thermal stability characteristics of jet fuels was declared the referee technique by jet fuel specification bodies.
This new approach highlighted the weaknesses of the existing thermal jet fuel oxidation test rigs. By precisely mapping the thermal oxidation deposit on the surface of the aluminum tube, it became possible to identify issues with existing test rigs that were undetectable with the visual (VTR) rating.
Based on these finding, AD Systems developed a new jet fuel thermal oxidation test rig (TO10) that ensures perfect fuel preparation, perfect fuel flow control, a perfect heater tube temperature profile and perfect thermal deposit quantification with the Deposit Rater - DR10.
State of the art automation level
Dual 5 mL syringe fuel pumping system, perfect fuel flow control, no pulse
Automatic fuel aeration control
Didactic and intuitive man-machine interface
Independant bus bar temperature control, no cooling liquid
DR10 - ITR connectivity for automatic result storage
No operator exposure to fuel vapor with safety door and fume extraction
Application
Refineries
Special fuel
Pipeline and terminals
Military fuel testing
Jet fuel testing
Specification
Technical Specification | Description |
Test method | ASTM D3241, IP 323, ISO 6249 Up to 21 customized test methods |
Test Temperature | Programmable from 100°C up to 380°C |
Differential Pressure | 0 - 750 mmHg (automatically bypassed at +700 mmHg) |
Test time Range | Programmable from 4 to 600 minutes |
Fuel Aeration | Programmable time, automatic air flow and control Efficiency of dessicant check with a humidity sensor |
Aeration Flow rate | Programmable or according to test method, 1.5 L / min |
Air Flow Humidity | Long live Dessicant Cartridge with humidity sensor. Automatic control and alert for the dessicant replacement |
Heater tube temperature measurement | Thermocouple Type K, class 1 Closed test compartment with sliding door prevent from air draft and assure steady temperature during the test |
Fuel Flow | Dual 5 mL syringe, maintenance free, programmable fuel flow rate or according to test method Accuracy ±1% No flow pulses or peaks |
Bus Bar Cooling | Heat pipe fluid technology + Peltier modules Each bus bar independently controlled to maintain consistent temperature profile test to test. |
Heater tube section assembling | Special gauge helps operator in quick and perfect position of the heater tube. Specialy engineered tube clamps assure repeatable surface contact and current conductivity. |
Fuel vapor handling | Dedicated compartment with sliding doors acting like fume hood encompassing beakers and heater tube section, connectable to a fume extractor |
Diagnostic and Service | Dedicated service menu with a flow chart diagram. Simply click on each element to check its operation. |
DR10 - ITR connectivity | Full test results can be automatically transferred from the DR10 to the TO10 Via Ethernet TCP/IP |
Results storage | Result database Limited only to capacity of external device |
LAN connectivity | Ethernet TCP/IP Combined TO10 & DR10 tube rating can be transferred |
Printer output | USB (printer is optional) |
Data output | USB (2), Ethernet port RJ45 |
Dimensions (mm) | 440 x 600 x 670 (17" x 23" x 26") |
Weight | 60 kg (133lbs.) |
Electrical | 100 to 240V - 8 A - 50/60Hz |
Operating temperature | From +10 to +35°C |
Relative humidity | 20% to 90% non-condensing |